MS-21 assembly line warming up. More pics in link:
https://sdelanounas.ru/blogs/96892/
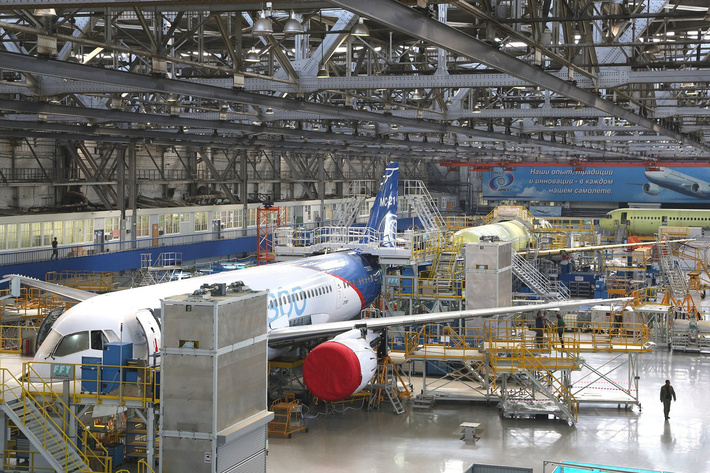
marat wrote:https://sdelanounas.ru/blogs/97386/#cut
Summer break is over and after more then one month new SU-100 is finnished. 19th this year, same as for whole last year 137 in total.
But still no new export contracts, no news regarding Zambia, Egypt and Iran orders or for potential sale to Slovenia ( 12 to Adria) .
PapaDragon wrote:marat wrote:https://sdelanounas.ru/blogs/97386/#cut
Summer break is over and after more then one month new SU-100 is finnished. 19th this year, same as for whole last year 137 in total.
But still no new export contracts, no news regarding Zambia, Egypt and Iran orders or for potential sale to Slovenia ( 12 to Adria) .
They still need to build ~300 of them before they run out of orders.
They can use the time to ditch imported parts. SSJ is product of it's time but that time is long gone. Time to update it.
PapaDragon wrote:marat wrote:https://sdelanounas.ru/blogs/97386/#cut
Summer break is over and after more then one month new SU-100 is finnished. 19th this year, same as for whole last year 137 in total.
But still no new export contracts, no news regarding Zambia, Egypt and Iran orders or for potential sale to Slovenia ( 12 to Adria) .
They still need to build ~300 of them before they run out of orders.
They can use the time to ditch imported parts. SSJ is product of it's time but that time is long gone. Time to update it.
marat wrote:PapaDragon wrote:marat wrote:https://sdelanounas.ru/blogs/97386/#cut
.....
They still need to build ~300 of them before they run out of orders.
They can use the time to ditch imported parts. SSJ is product of it's time but that time is long gone. Time to update it.
I am not sure that they have 300 orders at this moment
The Central Institute of Aviation Motors (CIAM CIAM named after PI Baranov), which celebrated its 85th anniversary at the end of last year, is rightly considered the leading research organization of the aircraft engine building industry in Russia. The institute carries out a full range of research from fundamental and applied to engine testing in conditions as close as possible to operational ones, and also scientific support of all domestic developments in this field. In cooperation with the enterprises of the United Engine Building Corporation, CIAM participates in the design, development and certification of all Russian aircraft engines. The newest generation of turbojet engines for passenger and transport aircraft, the PD-14, is the first for all post-Soviet years to become an exception. On the work of the Institute on this engine and other promising areas of development of domestic aircraft building, Vzlyot spoke with the Director General of the CIAM Ts. P.I. Baranova "by Vladimir Babkin.
Vladimir Ivanovich, the PD-14 engine, which entered flight tests last fall, became the first civil turbojet of the new generation, developed in Russia after the collapse of the USSR. It is known that in the formation of its concept, development and testing, CIAM implements them actively. P.I. Baranova. Please tell us about the most important points of your institute's work on this project.
The work of the CIAM on a promising engine family, the first in which the PD-14 has now begun to be tested, began in 1999 with the development, jointly with TsAGI, of a technical design for applied research for a new generation turbojet engine. In 2000-2002, Together with the Perm Aviadvigatel JSC, the rational technical appearance of a prospective two-circuit engine with direct drive of a fan was formed, and since 2004 a program for creating a scientific and technical reserve for the development of its development has been implemented. This work CIAM conducted jointly with other leading industry institutions - VIAM, VILS, TsAGI - and enterprises of domestic engine building.
Scientific and technical reserve was created for all the key elements of the engine - a low-noise wide-chord fan, a high-pressure high-pressure compressor, a low-emission combustion chamber, chevron nozzles of various types. A large complex of work was carried out on the combustion chamber and turbine. New technical solutions, implemented on the basis of scientific research, were tested on CIAM stands.
Created by the beginning of development work on the PD-14 engine, the scientific and technical reserve allowed to lay down in its design a number of new solutions for domestic engine building that should ensure its competitiveness in the world market. It should be noted that at the stage of ROC on PD-14 within the framework of the JDC, a wide cooperation of domestic engine building enterprises was formed, while Aviadvigatel OJSC was designated as the lead developer, and CIAM - responsible for scientific and technical support of the works and co-executor in the development of all major units and engine systems.
In particular, in the institute, in cooperation with Perm colleagues, aerodynamic designs of a fan and a high-pressure compressor were performed. The model of the fan with retaining stages passed a test complex at our stand C-3A (now it is working out the measures to minimize fan noise). For the high-pressure compressor, several standard stages were experimentally tested in the CIAM: the first supercharged, middle and closing ones, on which the blades of different profiling (sickle and saber-shaped) were tested, their different combinations in the guiding apparatus and in the impeller, etc. At the stands UV-13 and Ts5-2, complex tests of the full-size combustion chamber were carried out, during which the specialists of CIAM and Aviadvigatel checked its operability in all modes, optimal fuel supply scheme has been determined, reliable start in flight conditions, a wide range of combustion in the low-gas mode, required unevenness of the temperature field are ensured.
A significant role in the provision of the required parameters of PD-14 was played by the expertise of the CIAM experts of high and low pressure turbines with the development of recommendations for their gas dynamic development. At the TC-2 stand, several design variants of both turbines were tested.
The major milestone in the course of the PD-14 program was the testing of the full-size engine started on the high-altitude stand C-1A of the CIAM Research and Test Center in the Lytkarino suburb near Moscow that allows simulating the entire range of flight conditions in which the engine will be further operated. In Russia, only our institute has such a stand. The first stage of the PD-14 tests at our high-altitude stand, during which the specified flight conditions were simulated at an altitude of 11 000 m with the M = 0.8, was completed in December 2015.
The high-speed characteristics of the engine were investigated, its controllability and starting characteristics, the thermal state of the structural elements and the operation of the cooling system in high-altitude conditions were estimated. The second stage of the tests is being prepared,
On the waiting list there is still work to test the fan PD-14 at the stand T14-01 for checking the localization of fracture when the blade is broken and with the casting of a large poultry, accelerating and equivalent-cyclic testing of the rotor parts at the RS-1D stand, fire tests of hull parts, and various units at the stand C17-G3, etc.
In addition, CIAM is engaged in the development of normative documentation and methods for carrying out strength studies, as well as directly testing the structural strength of materials - in fact, a significant number of new alloys are used on PD-14.
As you can see, the scope of work of our institute under the PD-14 program is very significant. I hope that the successful completion of all the foreseen tests, a significant part of which takes place in the CIAM, will allow the certification of the engine to be completed within the stipulated timeframe - in 2017.
What difficulties did you encounter in the work on PD-14? Have you managed to realize all that was conceived? Could you assess the level of perfection of PD-14 against the background of existing western competitors? Does it have advantages?
The main difficulty was due to the fact that at the time of the start of development work on PD-14 due to extremely inadequate funding in previous years, the scientific and technical reserve of a high level of technology readiness for a number of nodes and systems was not created in time. As you know, the engine of the new generation is created 1,5-2 times longer than the airframe, and OCD on PD-14 began 5 years later than the start of works on MS-21 (2005).
At the same time, in the course of development work, in a number of cases it was necessary to create not "advanced", but "catching up" the scientific and technical backlog, which led to delays with the approval of the typical engine design ensuring the fulfillment of all the requirements of the technical assignment. In this regard, the term of certification PD-14 had to be postponed to 2017, and on the first flight the MS-21 will rise not with the domestic engine, but with the American PW1400G. There are still many works on PD-14, however, there are positive trends.
If we compare the PD-14 with the PW1400G, then, recognizing that we are likely to yield somewhat in economy, we can not fail to note the smaller mass and diameter of the PD-14, and, consequently, the smaller external aerodynamic resistance of the domestic power plant. In addition, we have a lower gas temperature in front of the turbine, which simplifies the achievement of specified reliability and resource parameters. In addition, PD-14 is much cheaper than a western competitor and, according to preliminary estimates, will have lower costs for maintenance and repair. In general, the direct operating costs of the MS-21 aircraft with a domestic power plant may be about 2.5% lower. This is important for airlines-operators. But the main thing is not even that. The program PD-14 has become a kind of locomotive for the development of domestic aircraft engine building. After,
It is known that PD-14 should be the first in a family of promising new generation gas turbine engines. What, in your opinion, are the priority directions for modifying the basic engine?
Indeed, our institute is currently performing a large amount of work related to the plans for the further development of the PD-14 engine and the development of its modifications. First and foremost, this PD-14M with increased to 15.6 tons thrust and turbo PD-12V for heavy helicopters. In addition, the possibility of creating a reductor turbojet with a thrust of 18.7 tons - PD-18R and, conversely, less powerful turbojet engines for regional aircraft - PD-10 (10.9 ton-force) and PD-7 (7.9 tons) is being explored. On the basis of the PD-14 gas generator, it is planned to create also a line of ground-based industrial engines - for driving power plants and gas pumping units.
In the framework of studies on more powerful modifications of the PD-14 in the CIAM, work is under way on a fan with polymer composite working blades and on a reducer, which may be required for its drive.
At the last jubilee scientific and technical conference "Motors of the XXI century" held at the CIAM at the end of the jubilee scientific and technical conference "Aviadvigatel" OJSC and Samara JSC "Kuznetsov" presented their proposals for the creation of new turbojet engines for the remotorization of the heavy An-124 " Ruslan "and equipment of perspective wide-body aircraft. How does CIAM view a prospective TRDD with thrust of 30-35 tons? Does the institute already work in this area?
As is known, the domestic aviation industry currently does not produce two-circuit turbojet engines for passenger and transport aircraft with a thrust of more than 16-18 tons. At the same time, in order to maintain the competitiveness of Russian heavy-lift transport aircraft and to return our country to the market of long-haul wide-bodied aircraft, we need to create our own basic turbojet engine with thrust of 30-35 tons. We believe that it should be done on the basis of a unified gas generator, which can serve as the basis for a wide range of aircraft engines with thrust from 20 to 40 tons and power plants with a capacity of 30-60 MW.
In 2014 our institute, with the participation of TsAGI, UDK and Aviaprom OJSC, was entrusted with carrying out the research work "TRDD-30" ("Research in the field of creating a large thrust turbojet on the basis of a unified gas generator for perspective wide-body passenger and transport aircraft civil aviation "). In the framework of this research, the technical requirements for a high-thrust engine have been clarified, research has been carried out to determine its technical appearance and a list of critical technologies, and new models of scientific and technical solutions and technologies have been developed on models and experimental models.
Among the critical technologies that, in our opinion, it is necessary to implement to create competitive engines of this class is the creation of a fan of light polymer composite materials with an ultra-low peripheral speed of rotation (this will reduce the mass of the fan by 30% compared to the technology of hollow titanium blades, used on the PD-14 and significantly reduce the noise level), new low-emission combustion chambers, high-performance turbines.
Increasing the maximum total pressure build-up in compressors to about 60 will reduce the specific fuel consumption. Creating a highly efficient and reliable gearbox that transmits power to 50-60 MW with an efficiency of at least 99% will ensure a reduction in the number of stages of the turbine by half and a reduction in engine noise by 6-8 EPN dB. It is also necessary to work a lot in the part of creating new technologies for the manufacture of engine parts from advanced structural materials - intermetallides, incl. titanium aluminides (casings, blades, etc.), ceramic composites (parts of a turbine and combustion chamber), metallic composite materials (elements of fastening elements and shafts).
All this will require the implementation of a broad front of research in the framework of the state program "Development of the aviation industry for 2013-2025." Bringing new technologies to the 6th level of technological readiness with the creation and testing in a thermo-chamber of a high-altitude test stand of an experimental universal gas generator and demonstration engines will require modernization and creation of new stands for experimental research and testing of engines, their units and systems, including a new flying laboratory (for example, base An-124).
What is the general view of the CIAM line of domestic civil aircraft engines for the medium term? Is there already an understanding of how to further develop engines for passenger and transport aviation, for helicopters?
Today in CIAM, on the basis of the adopted system of levels of technological readiness, a long-term program for the creation of a scientific and technical reserve for engines of various classes and purposes has been formed. We believe that by 2020, up to the 6th level of technology availability, improved versions of PD-14 (for MS-21) and TV7-117 (for regional aircraft) should be brought.
For the next five-year period, by 2025, this draft level should be reached by the projects of a new turbojet engine with a thrust of 22 tons (for transport aircraft), based on the PD-14 PD-10 engine (for SSJ100 aircraft), and a new turbojet (for regional aircraft). Approximately by 2030 to the 6th level of readiness of technologies it will be possible to bring the program of a new TRDD with a thrust of 35 tons for long-haul aircraft,
In the part of helicopter powerplants we expect that by 2020 an improved (based on VK-2500) can be prepared, and by 2025 - and a fundamentally new (MPE) turbo-engine in the class of 2500 hp. At the same time, by the middle of the next decade, the project of a turbofan PD-12V engine in a class of 10 thousand hp is possible. For light aircraft and unmanned aerial vehicles, by 2020, a diesel engine can be built in the 500 hp class. and a small piston engine at 50-150 hp. respectively, and by 2025 - turbo-compound piston engine in the class of power of 500 hp. For airplanes of local air lines and light GTE in the class of power 350 hp. for UAVs. By about 2025, we expect the readiness of a new auxiliary power plant with a capacity of 500-700 kW, and by 2030
By increasing the parameters of the cycle, improving the nodes, and introducing new materials (primarily composite ones), the engines for civil and transport aviation by 2020 should be 5% more economical on cruising conditions and 40-50% more environmentally friendly by emission of nitrogen oxides relative to level, achieved now on the PD-14. By 2025, economy and environmental friendliness should increase by 10 and 60%, and by 2030 - by 20 and 65% to today's level, respectively. In parallel, the noise level will be consistently reduced.
The reduction in the specific fuel consumption of helicopter engines, relative to today's VC-2500, is estimated at 5% by 2020, by 7% in 2025, and by 10% by 2030. This will be achieved by increasing the cycle parameters, applying dust protection devices with a high degree of purification, high-speed axial and centrifugal compressors, a multi-fuel low-emission compact combustion chamber, a high-speed, highly loaded single-stage compressor turbine, a free turbine with the opposite rotation of the rotor, an electric drive FADEC type combined with the system diagnostics, new materials, types of seals and bearings.
This is our forecast for the development of aircraft engine technology for the next 10-15 years. I hope that the great experience that has been accumulated in the eight and a half decades of CIAM's work, our scientific potential and effective cooperation with industry-leading enterprises and serial plants will make it possible to translate our forecasts into real aircraft engine projects for domestic aircraft and helicopters.
Firebird wrote:Has anyone managed to figure out how the Sino-Russian widebodied jet will be done?
I know final assembly is in China, and Russia will do most of the design/tech work.
But will Russia be giving technology transfer? Will Russia be assembling its own?
What will the terms be for selling to 3rd parties?
Will it be like Brahmos vs Zircon missiles ie Russia helps with an Indian variant, and builds Zircon for itself? In other words will the joint venture be Russian-Chinese, and Russia builds her own plane separately?
PapaDragon wrote:Firebird wrote:Has anyone managed to figure out how the Sino-Russian widebodied jet will be done?
I know final assembly is in China, and Russia will do most of the design/tech work.
But will Russia be giving technology transfer? Will Russia be assembling its own?
What will the terms be for selling to 3rd parties?
Will it be like Brahmos vs Zircon missiles ie Russia helps with an Indian variant, and builds Zircon for itself? In other words will the joint venture be Russian-Chinese, and Russia builds her own plane separately?
Design and development in Russia, wings manufactured in Russia (composite wings most likely just like MS-21), fuselage made in China, engines and avionics Russian or Western per customer request (again, like MS-21), assembly in China and then delivery to customer.
Firebird wrote:............
OK but what happens if they fell out in 10 years time?...
Firebird wrote:...Or if Russia wanted to build a slightly different variant/enhanced one?
The Russian Helicopter Systems (RVS) company reported on October 19, 2017 that it received another Ansat helicopter with a medical module. The new helicopter with the registration number RA-20006 was produced by the Kazan helicopter plant (KVZ) of the holding company "Helicopters of Russia", and its medical module was manufactured by the Kazan assembly plant. The helicopter will be involved in the implementation of the priority project "Ensuring Timeliness in Providing Emergency Medical Aid to Citizens Living in Hard-to-Access Areas of the Russian Federation".
KomissarBojanchev wrote:Why doesn't Russia sell the SSJ100 with american components to Iran anyway? Its not like anyone will give a shit.